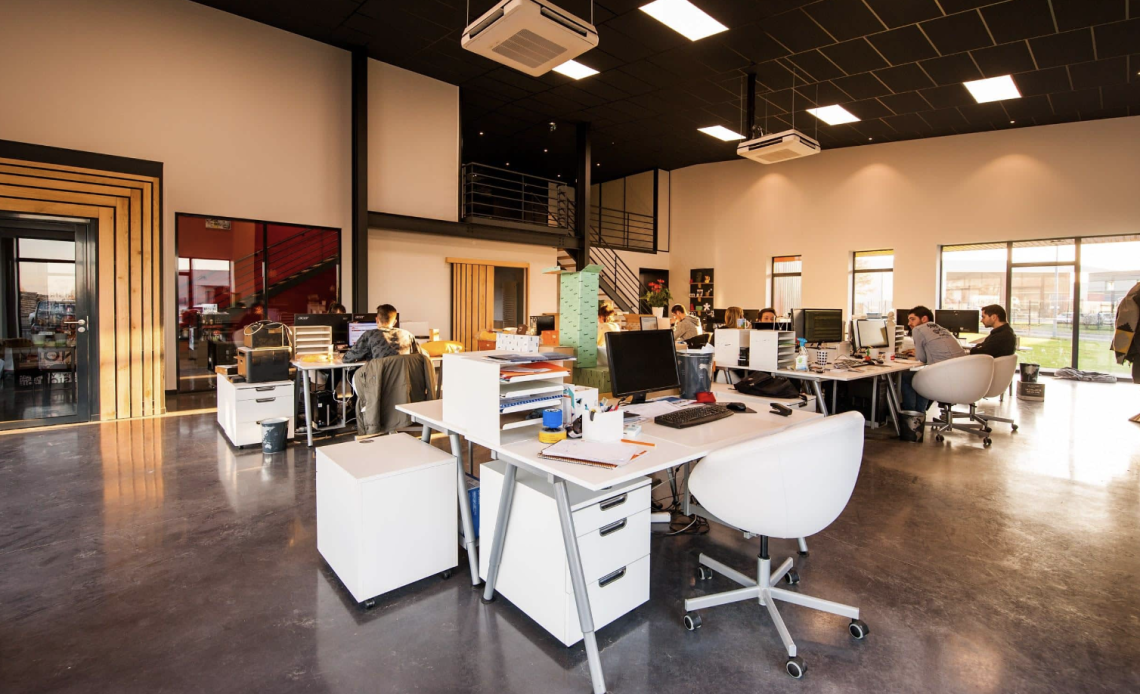
While deliberating on labelling solutions, it is crucial to ensure that you know both solutions in mind to ensure you are sure of the answer you are willing to utilize before deciding on a solution. Two printing technologies may affect the labeling solutions you intend to use. The two printing methods include; direct thermal and thermal transfer. A thermal printhead is used in each approach to applying heat to the area being printed. Thermal transfer printing employs a ribbon to create long-lasting, durable graphics on various surfaces. Instead of using a ribbon, direct thermal printing generates the image directly on the printed substrate.
Choosing the proper labels tailored for your printing and use scenario is critical for seamless and successful operations. When you start with the appropriate label selection, you’ll save time and money by printing accurately and extending the life of your printer. Selecting a printing and labeling solution appears to be a daunting task. However, choosing the right printing solution for your labeling requirements may save you thousands of dollars in terms of time and inventory management.
It is critical to distinguish in today’s highly competitive world. As a result, white-label solutions were created by marketers. Business owners prefer white-labeled software and apps to those with autonomous branding. Because of the quick advancement of technology, white labeling is becoming more and more common with each passing day.
Here are some of the factors to consider when choosing labeling solutions for your needs
1. Mobility of Products
Examine where your items spend most of their time. Identifying the day-to-day operations of your product can assist you in determining the type of label material and mobile printing solution you require. If your items are exposed to the elements, you should consider using thermal transfer synthetic material. When it’s time to shift things again provides durability and flexibility. They’re among the most demanding portable gadgets on the market, operating even when staff is wearing gloves. On the other hand, direct thermal labels are best for indoor items.
2. Consider the environmental needs such as weather and temperature.
Label adhesion is critical, as excessively hot or low temperatures can diminish the label’s effectiveness. It makes a difference if you apply the title to the item at 75°F and then transport it to a -2°F freezer afterward. Ordinary solutions are OK if labels are used above 25°F and moved to temperatures between 65°F and 200°F; simple solutions are OK. You’ll require thermal transfer supplies and probably a unique adhesive for degrees beyond those limits. The ZQ500 series from Zebra is one of the most resistant to severe temperatures, with devices that can withstand temperatures ranging from -4°F to 131°F.
3. Chemical and abrasion resistance
Abrasion can cause labels to become unreadable and worthless. Choosing label ribbons with greater resin concentrations helps extend the life of your brands. Similarly, you should pay attention if labels are near chemicals, no matter how harsh or seemingly benign (yes, even water). Consider thermal transfer material if your items will be exposed to mild or weak chemicals (bleach, alcohol, water, window cleaners). When subjected to severe chemicals, a resin ribbon would be perfect.
4. Printer and label quality
Make this a priority if your labels must be printed within a specified time frame. Print speeds are directly proportional to the label material you employ. Synthetic material, for example, will not print in excellent quality at rates greater than 6 inches per second (IPS), and To print at rates faster than 12 ips, you’ll could use a special high-speed wax ribbon. If you wish to print quickly, raise the darkness to guarantee good barcode quality. Because print darkness should be high at faster print speeds, using better-grade ribbons consumes more energy and ink. Finally, dots per inch (DPI) is critical for labels with small letters or intricate illustrations. If that’s the case for your company, you’ll need a synthetic fabric that’s highly smooth or shiny.
5. Application of the Applicator
If one intends to employ an applicator then it must be indicated ahead of time since the label must be cut differently to peel away from the liner correctly. Furthermore, perforations are not normally recommended since they affect the liner’s stiffness qualities, making it more difficult to remove.
6. Chemical Resistance
A thermal transfer labeling solution is necessary when a label will be subjected to moderate or harsh chemicals. A high-durability resin ribbon is also advised in the case of severe and extreme chemicals.
7. Resistance to Abrasion
Over time, contact and rubbing will compromise reading. A ribbon with a unique resin content will give better resilience if the label may come into touch with goods on a pallet or during transportation that could damage it and render it illegible.
8 . The floor
To adhere to the surface, the kind and form of the surface to be labeled must be considered. Surface energies vary depending on the object. Small curved surfaces, for example, are more challenging to work with because they necessitate a flexible material with a strong mandrel adhesive to keep the barcode label from pulling away from the surface.
9. Speed of Printing
This is an essential factor since the material and ribbon you choose will affect the maximum print speed. Synthetic labels often do not create high-quality text and barcodes over six ips; thus, a thermal transfer paper label with a high-speed wax ribbon must print at 12 ips or above.
10. The darkness of the print
Increasing print darkness is required to achieve the best barcode grades and print quality when printing at higher speeds. You’ll need more darkness when utilizing higher-grade ribbons, which demand more energy.
In conclusion, these are just a few of the most important considerations when choosing the best label solution for your application. While labeling may appear to be a minor detail when running a big plant, it should not be disregarded. New improvements are also released regularly, which might bring prospects for better efficiency and durability. You’ve found the best label solution whenever your label materials and ribbons stay readable during storage, transport, and shipment. Regarding label choosing, don’t be afraid of the practically infinite possibilities.