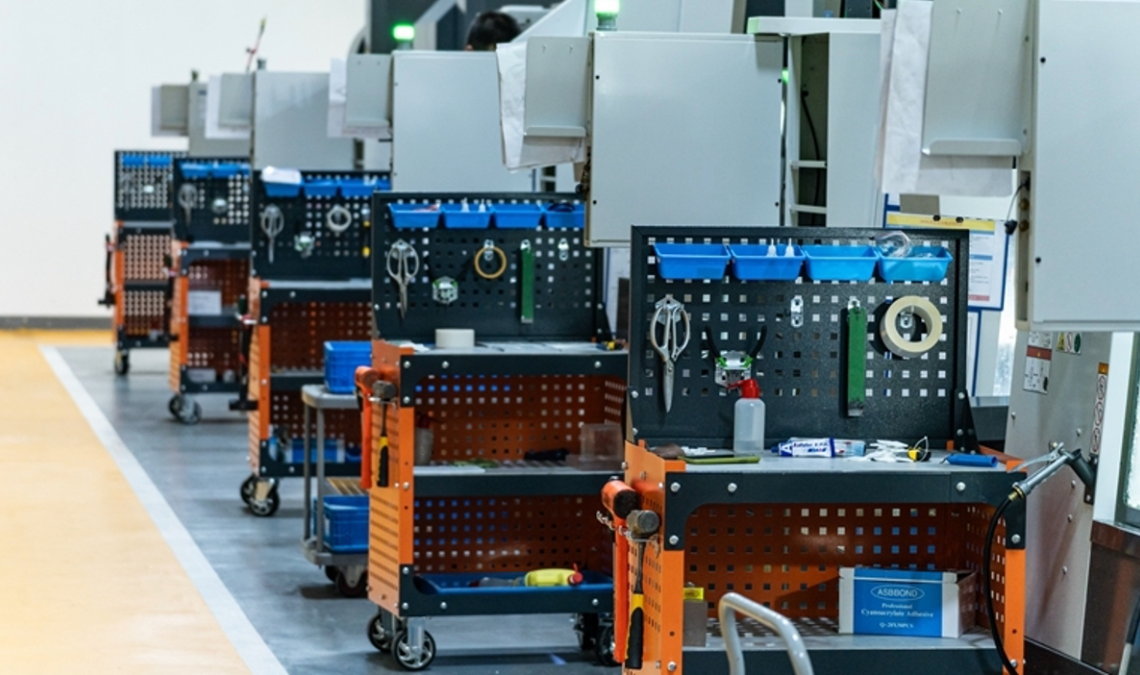
Since aerospace systems are moving towards more compact and power-dense structures, the expectations for the performance of electronic components are at the highest level. With the impetus toward miniaturization coupled with harsh requirements for efficient heat removal, the role of material choice as well as manufacturing accuracy has been made even greater. In that context, CNC aluminum is a clear winner and a preferable choice because it has the best mechanical properties (strength), lightweight properties, and excellent heat conductivity.
Moreover, the accuracy of CNC machining facilitates the manufacture of customized machined parts to the complex geometrical requirements of modern aerospace electronics. These customized units add synergy and efficiency to the integration and operation of the system, making them work optimally even under complex conditions.
1. Miniaturization Demands High-Precision Manufacturing
Aerospace electronics are becoming more sophisticated at rapid rates, whereby engineers are tasked with performing more functionality in reduced spaces. It is a trend that accelerates – from advanced avionics systems and satellite communications units to drone flyer controllers to the embedded Nav modules. In these applications, there is almost no scope for dimensional errors. All cubic millimeters need to be carefully engineered, and the components must interlock to near-perfect matches to provide the full system integrity and performance.
CNC aluminum is crucial in overcoming such constraints because components with very high precision and a serious level of tolerance can be produced. It lends itself, in particular, to the production of lightweight enclosures, internal brackets, sensor housings, and other structural components that have to carry small arrays of printed circuit boards and microelectronic components.
Unlike cast or injection molding parts that could be warped, shrunk, or not all that accurate, CNC machining is precise batch after batch. This makes it the perfect solution for custom-made parts that have to fit perfectly into closely packed assemblies. From functional prototypes to low-volume production series, CNC aluminum equates to repeatability, stability, and fidelity to the design at every step.
2. Thermal Conductivity That Supports High-Power Density
With aerospace electronic components becoming faster and producing greater power as they function, heat management has become an important aspect of system design. Insufficient heat dissipation may cause many problems, including signal interference, low performance, or total system failure. These dangers are escalated in the aerospace environment where airflow is restricted, and cooling strategies are usually encumbered by weight and size requirements. This is exactly where CNC aluminum comes in handy.
Aluminum is well known for its ability to conduct heat from sensitive electronic components. Combined with CNC machining, this can be formed exactly into housings that have integrated heat sinks, thermal channels, or tailor-configured fins. These attributes assist the extraction of heat from the fundamental circuitry, ensuring stable performance despite the continuous operation.
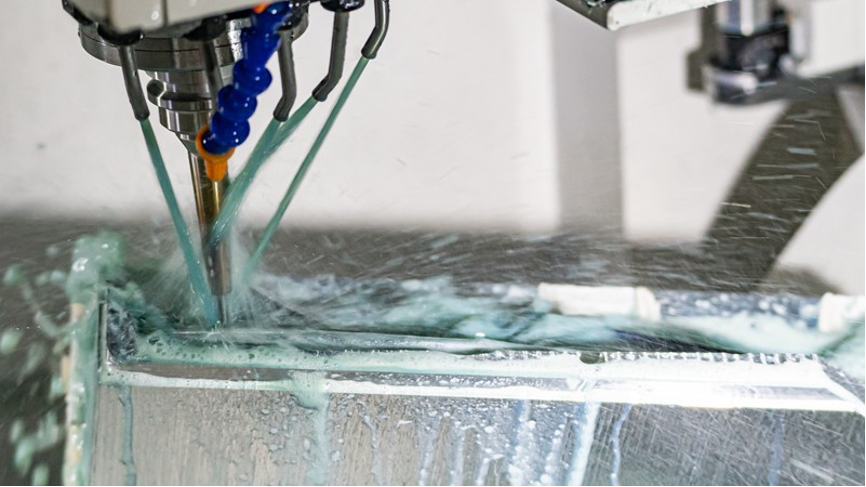
Since CNC machining provides precise control on CNC design aspects such as wall thickness, air flow vents, and surface area improvements, engineers can engineer custom machined parts to satisfy spatial and thermal requirements,without expanding the footprint or violating system integrity.
3. Material Advantages: Lightweight, Durable, and Corrosion-Resistant
In aerospace electronics, selecting the right material involves balancing electrical performance, structural integrity, and environmental durability. Weight limitations are always a crucial point however the components must still be able to stand vibration, temperature extremes, radiation, etc. CNC aluminum provides a versatile solution to all of these demands.
High-performance alloys that include 6061 and 7075 offer very good strength-to-weight ratios, and are ideal for enclosure, mounting brackets, and structural supports that also need shielding or grounding prowess. These aluminum grades are corrosion-resistant by nature, which is quite significant in aerospace environments under the effects of moisture, salt mist, and space radiation.
One more major benefit is that aluminum can be used with surface treatments like anodizing, which enhances electrical insulation, durability, and final look. From the manufacturing point of view, the superior machinability of aluminum ensures accurate cuts, fine internal detail, and trustworthy threaded holes. When producing custom machined parts, CNC aluminum ensures consistent quality across batches, even with tight tolerances or intricate geometries. This reliability is especially important while designing the components which should comply with the aerospace certification and long-term performance standards.
4. Prototyping and Production Agility for Aerospace Innovation
Aerospace programs usually require emergent design development from concept models to airworthy hardware in a hurry. The capability to quickly convert a digital design into a physical part, without waiting for tooling or in a long production setup is a requirement to meet the schedule. This speed, and the ability to rapidly adapt, are made possible with the help of CNC aluminum in every step of development.
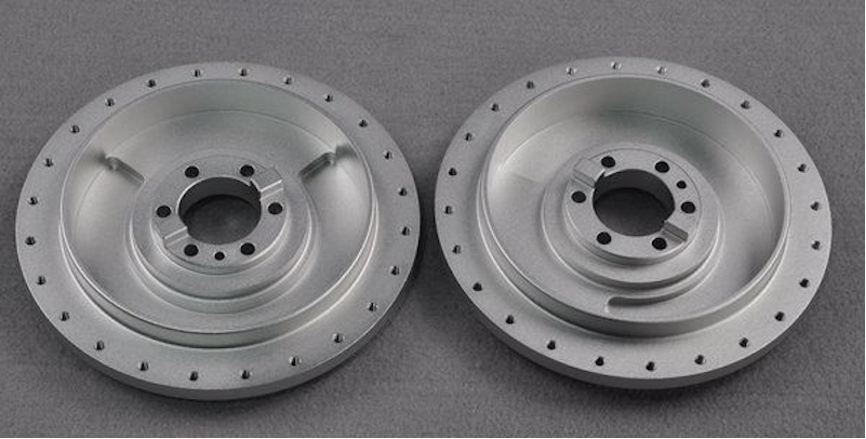
Engineers can move from CAD to a prototype only in a few days with sophisticated digital manufacturing workflows. These custom machined parts can then be tested for their performances in actual operating environments concerning their thermal performance, mechanical integration as well and electromagnetic interference shielding. When alteration needs to be done, the design can be altered and re-machined without any delays and/or tooling. This speeds up testing and iteration without blowing the budget.
Further, CNC aluminum facilitates an easy shift from prototyping to full-scale production. The same machining strategies employed in initial versions can be extended to larger quantities without changing the part dimensionalities and performance. This is an important continuity given that the aerospace components will be subjected to rigorous standards such as the AS9100 without compromising agility and precision.
Conclusion
Miniaturization and thermal management are key challenges in today’s aerospace electronics. CNC aluminum offers an ideal solution by combining excellent machinability, thermal conductivity, and strength. It enables the production of custom-machined parts that support tight integration, efficient heat dissipation, and structural reliability in compact systems. As aerospace technology continues to advance, CNC aluminum remains a critical material for achieving performance targets, supporting rapid development cycles, and meeting stringent industry standards for reliability and precision.